无尘车间的建造,除考虑实用性及可靠性外, 强调灵活性以适应集成电路 更新换代快的要求, 使原有无尘车间能方便的迅速的按生产要求进行调正及改造 。
已有研究提出对硅片的自然氧化及硅片表面吸附的分子需要进行控制, 硅片的加工需在高纯氮或高真空的洁净区内,硅片的传送亦需在高纯氮的洁净环境内, 即集成电路微加工需在封闭系统内进行 。
【车间设计铜的型材产品方案 车间设计铜的型材产品方案怎么写】集成电路无尘车间是为了满足半导体制造工艺需求的洁净室 , 该无尘车间对环境洁净度、温湿度、振动、ESD、AMC控制等都有一定的要求 。相对于其他工业洁净室 , 集成电路制造无尘车间有面积大、洁净等级高、温湿度控制精度高等特点 。
根据洁净室车间空气循环特点可以将洁净室分为三种类型:循环空调机配合高效送风口系统、循环风机配合湿式密封系统和FFU循环系统 。
1. 小规模低等级要求的洁净室车间设计中被广泛应用 , 对于大面积高等级的洁净车间则存在运行成本过高、占用空间过大等缺点 。
2. 设计可以满足集成电路制造无尘车间大面积高等级的要求 , 但运行成本较高 , 并且洁净室风速、风量调节困难 , 系统升级改造困难 , 因此操作灵活性很低 。
3. FFU循环系统不仅节省运行空间、洁净度安全性高、运行成本低 , 而且操作灵活性很高 , 可以在不影响生产的情况下随时进行系统升级和调整 , 这些都能很好地满足半导体制造的需求 , 因此在半导体制造业FFU循环系统逐渐成为最主要的净化设计方案 。
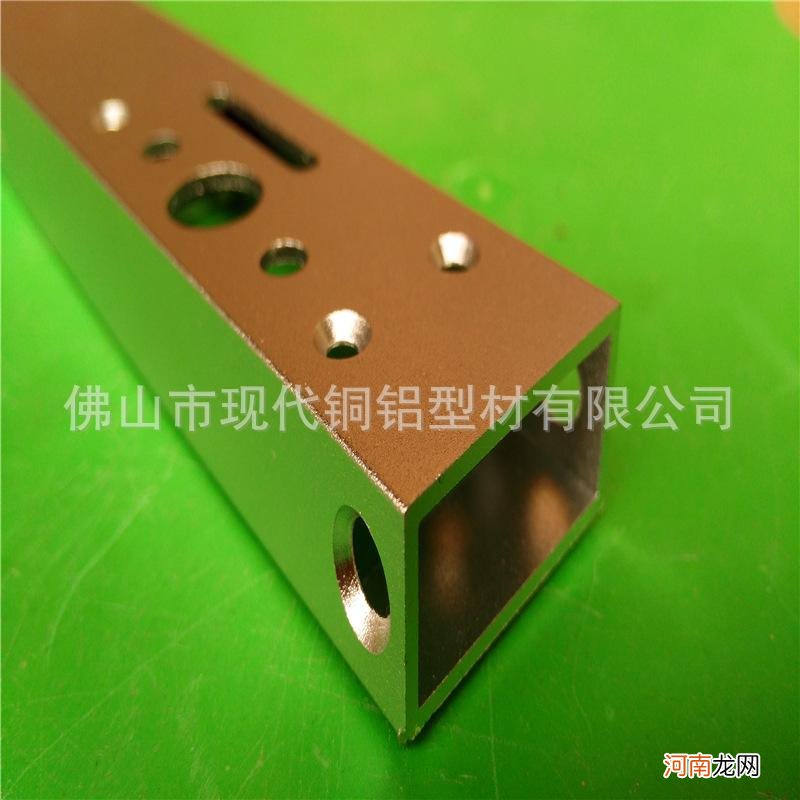
文章插图
根据已有的研究, 生产集成电路的洁净区内悬浮粒子的来源情况如下:
≥0.5μm的粒子主要来自无尘车间内工作人员、洁净服、转动机械、无尘车间用品及物体表面的振动等;
0.1一0.5μm的粒子主要是由室外空气中的粒子穿过过滤器而漏人无尘车间的;
<0.1μm的粒子(超细粒子) 主要由燃烧或蒸发后的物质均相聚集或冷凝引起的, 因此, 无尘车间内工艺设备的加热元件、线路版上的元件、受热轴承、电机、火焰及热的光都是其来源 。而超高效过滤器对这种粒子几乎可以全部过滤掉 。
根据已有报导, 有关集成电路亚微米加工在l级( F S 一2 09 D ) 无尘车间内( 即洁净度为≥0.5μm的粒子不多于7 个/ft3), 相应于≥0.1μm的粒子不多于35 个/ft3,测得硅片上的污染粒子来源及比例情况如下:
1. 操作人员(穿洁净工作服) 引起的, 如片盒传送及操作、走动的交叉污染等占30% ;
2. 工艺介质带人的占23% ;
3. 工艺设备引起的, 如本身的及交叉的污染占20% ;
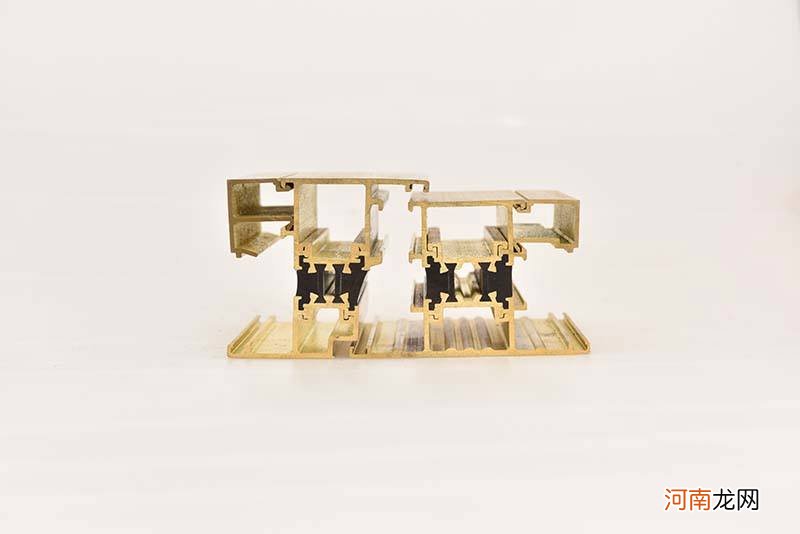
文章插图
4. 工艺加工引起的, 如工艺加工本身的及交叉的污染占25% ;
5. 穿过超高效过滤器而漏人的占2% 。
根据以上例子及分析可以得出基本的认识是: 在亚微米加工的洁净区内, 洁净区的空态洁净度已不是影响动态洁净度的主要因素, 因为当前超高效过滤器的过滤效率对≥0.1μm粒子达9 9.9 9 9 5 一9 9.9 9 9 9 9 9 9% 的情况下,集成电路亚徽米加工的合格的无尘车间其空态沽净度为1 ~ 10 个/ft3(≥0.1μm粒子), 且往往检侧不到 。因此, 合景净化的洁净工程师认为 , 控制工艺本身、工艺设备、操作人员等散发的粒子污染当是主要矛盾 。而在100级的无尘车间≥0.1μm的粒子有3500个/ft3, 之多, 这种情况下, 当然空态洁净度会是影响动态洁净度的主要因素 。
- 西宁销售铜包钢接地棒 西宁销售铜包钢接地棒电话
- 数控铜铝型材自动切割锯床 铝型材数控切割设备
- 铜条砖 岩砖是什么砖
- 莱芜铜铝型材切割机 莱芜激光切割钢板对外加工
- 高压喷雾加湿系统方案设计 高压喷雾加湿系统方案
- 仿铜型材门 铝合金仿铜门厂家
- 铝型材仿铜拉丝门 仿古铜拉丝门图片
- 创业设计的内容包括多选题答案 创业设计课程平时作业1
- 山东挤压铜型材厂家 山东铝型材挤压厂家
- 变电站接地极如何设计电流 变电站接地极如何设计